Motivation and objectives
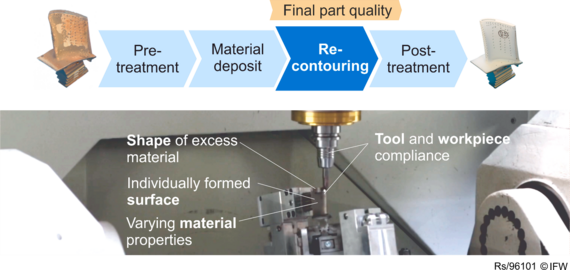
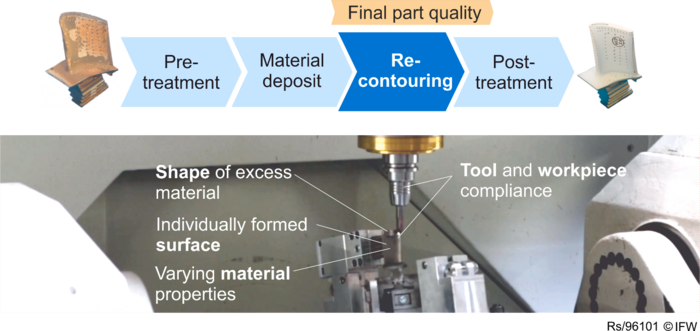
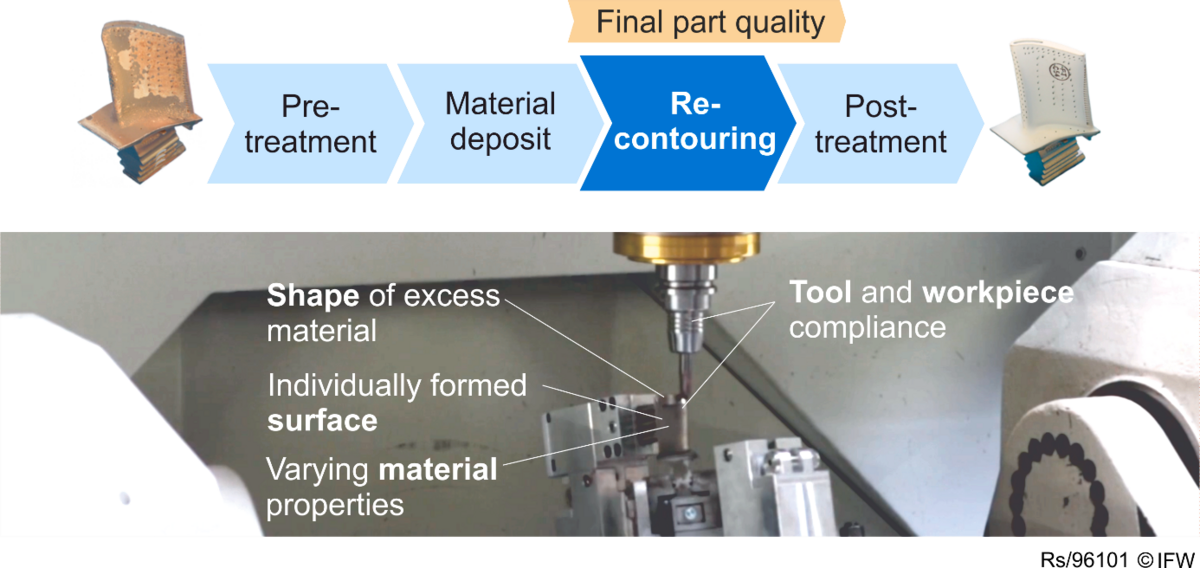
Due to its impact on the components function in relation to the entire system, the re-contouring is an important sub-process in repair of complex capital goods. Due to the individuality, each component of the capital good represents a batch size one process. Hence, in planning of the re-contouring process manual CAD/CAM methods are state of the art. This results in uncertain and unreproducible repair processes for each component.
The goal of the sub-project is an algorithm for the automatic planning of the re-contouring process. Inside the planning algorithm, an evaluation and adaption of the process is carried out. The aim is to gain part quality aspects that satisfy the requirements resulting from the functional review. The evaluation includes a geometric, dexel-based process simulation. Based on empirical process models, the individually simulated tool engagement conditions are correlated with quality parameters. The subsequent process adaption leads to a process that satisfies the required quality criteria for an individual component.
Please note that activating the video will result in the transfer of data to the respective provider. Further information can be found in our privacy policy.
Play video
Re-contouring of an analog blisk on the 5-axis milling center Deckel Maho DMU 125P
Results
A prototype for the planning algorithm has been implemented based on the simulation software IFW CutS, and an interface to a commercial CAM system. Within large experimental studies it has been shown which process parameters have significant impact on the subsurface of complex parts. Engine blades made of titanium and nickel base alloys have been the subject of investigation. Tool angles as well as cutting edge micro geometries have a major impact on sub surface residual stresses. Two geometric process parameters have been developed. The surface-generating forces enable the prognosis of process induced residual stresses. The surface generating cut volume furthermore leads to an evaluation of residual stresses induced part distortion for the considered material. This is of importance when re-contouring thin-walled compressor blades. These parameters allow the technological evaluation and adaption of individual re-contouring processes in the planning algorithm.

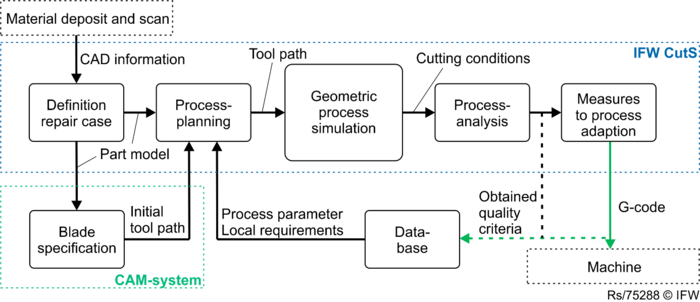
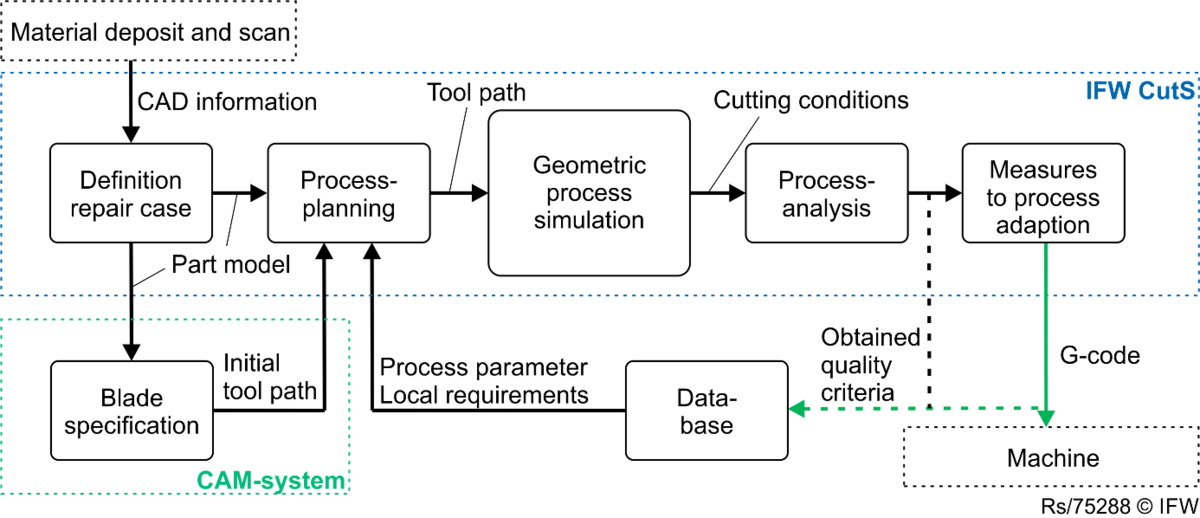
Current research and outlook
The aim of sub-project C1 in the 3rd funding period is to extend the automated process planning and simulation to the welding material application, and to improve the prognosis of surface quality after material removal. This will enable joint planning to take place for the first time, taking into account the technological interactions between the regeneration processes. A repair-specific data model is being developed in sub-project C1, which stores the necessary information of a process for an individual component and makes it available to all other processes with the addition of a tolerance. This CAD-based work piece dovetails with the intelligent work piece carrier developed in the 3rd funding period in sub-project B2 to ensure cross-process planning and optimization of the regeneration according to the roadmap of the Collaborative Research Centre.

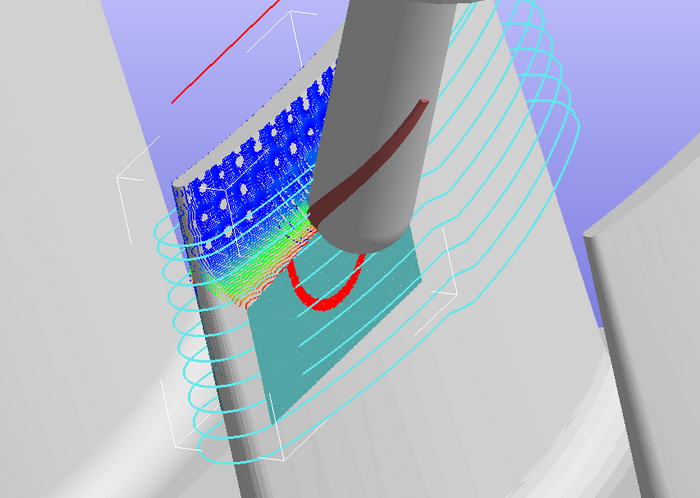
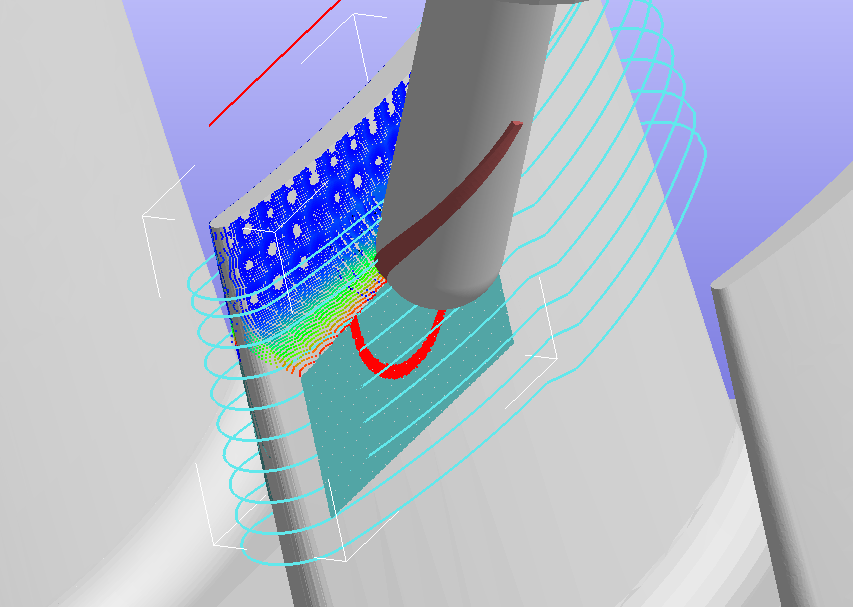
Subproject leader
30823 Garbsen
30823 Garbsen
30823 Garbsen
Staff
Publications
International Scientific Journal Paper, peer-reviewed
-
(2018): Technology-based Re-contouring of Blade Integrated Disks After Weld Repair, J. of Materi Eng and Perform 27, 2018 (1), 253-260
DOI: 10.1115/1.4040738 -
(2017): Design of individual re-contouring processes, Procedia Manufacturing 14, 76-88
DOI: 10.1016/j.promfg.2017.11.009 -
(2017): Residual stress formation after re-contouring of micro-plasma welded Ti-6Al-4 V parts by means of ball end milling, Materials Science and Engineering Technology 2017, 1034-1039
DOI: 10.1002/mawe.201600743 -
(2016): Repairing parts from nickel base material alloy by laser cladding and ball end milling, In: Prod. Eng. Res. Devel. 10 (4-5), S. 433–441
DOI: 10.1007/s11740-016-0690-7 -
(2016): Surface topography after re-contouring of welded Ti-6Al-4V parts by means of 5-axis ball nose end milling, Int. J. Adv. Manuf. Technol. 85 (5-8), S. 1585–1602
DOI: 10.1007/s00170-015-7885-5 -
(2015): Engine blade regeneration: a literature review on common technologies in terms of machining, Int J Adv Manuf Technol 81 (5-8), S. 917–924
DOI: 10.1007/s00170-015-7256-2 -
(2015): Differences and similarities between the induced residual stresses after ball end milling and orthogonal cutting of Ti–6Al–4V, Journal of Materials Processing Technology 226, S. 15–24
DOI: 10.1016/j.jmatprotec.2015.06.033 -
(2014): Residual stresses formation after re-contouring of welded Ti-6Al-4V parts by means of 5-axis ball nose end milling, CIRP Journal of Manufacturing Science and Technology 7 (4), S. 347–360
DOI: 10.1016/j.cirpj.2014.07.001 -
(2013): Numerical simulation of process forces during re-contouring of welded parts considering different material properties, CIRP Journal of Manufacturing Science and Technology 6 (3), S. 167–174
DOI: 10.1016/j.cirpj.2013.05.001
International Conference Paper, peer-reviewed
-
(2019): Advanced process design for re-contouring using a time-domain dynamic material removal simulation., 12th CIRP Conference on Intelligent Computation in Manufacturing Engineering (Hg.): Procedia CIRP 79 (2019), S. 21–26.
DOI: 10.1016/j.procir.2019.02.005 -
(2018): Ball end milling of titanium TIG weld material and the effect of SiC addition – process forces and shape deviations, 6th International Conference on Through-life Engineering Services, TESConf 2017. 7-8 November 2017, Bremen, Germany, Seite 74-81
DOI: 10.1016/j.promfg.2018.01.011 -
(2016): Prediction of the Principal Stress Direction for 5-axis Ball End Milling, Procedia CIRP 45, S. 291–294
DOI: 10.1016/j.procir.2016.02.145 -
(2015): Prediction of the 3D Surface Topography after Ball End Milling and its Influence on Aerodynamics, Procedia CIRP 31, S. 221–227
DOI: 10.1016/j.procir.2015.03.049 -
(2015): Simulation and Evaluation of Different Process Strategies in a 5-axis Re-contouring Process, Procedia CIRP 35, S. 31–37
DOI: 10.1016/j.procir.2015.08.059 -
(2014): Approaches for Improving Cutting Processes and Machine Tools in Re-contouring, Procedia CIRP 22, S. 239–242
DOI: 10.1016/j.procir.2014.06.148 -
(2012): Milling Simulation of Welded Aero Engine Components, Proceedings of the 3rd Machining Innovations Conference, S. 403–410
-
(2011): Kinematic and Stochastic Surface Topography of Machined TiAl6V4-Parts by Means of Ball Nose End Milling, 1st CIRP Conference on Surface Integrity (CSI), Bd. 19, S. 81–87
DOI: 10.1016/j.proeng.2011.11.083
National Scientific Journal Paper, not peer-reviewed
-
(2018): Prozessauslegung für die Regeneration komplexer Investitionsgüter, Unter Span, Ausgabe 2018, S. 22-23
-
(2016): Werkzeugwege für den individuellen Reparaturfall, In: phi 2016, S. 3.
-
(2010): Forschen am IFW: Nach allen Regeln der Zerspankunst, phi - Produktionstechnik Hannover informiert, 11 (2010) 2, S. 16-17
Dissertationen
-
(2015): Randzonenbeeinflussung durch die Rekonturierung komplexer Investitionsgüter aus Ti-6Al-4V, Berichte aus dem IFW, Band 07/2015, 111 S., PZH Produktionstechnisches Zentrum
ISBN: 978-3-95900-056-7