Motivation and objectives
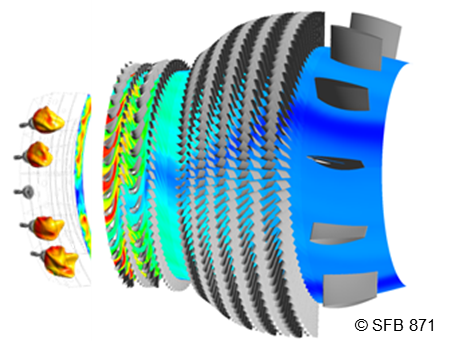
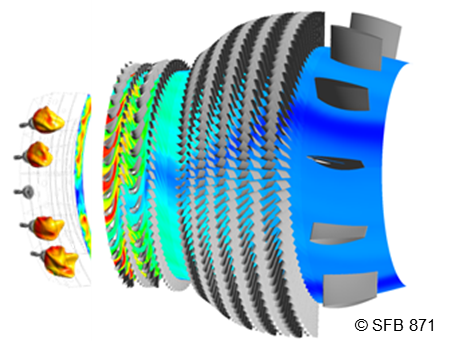
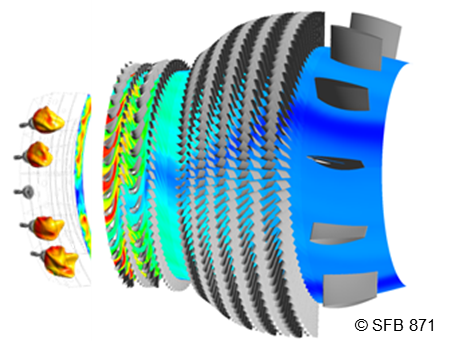
Defects in combustion chambers of aircraft engines might reduce the performance and represents an increasing stress of the turbine. The mixing is determined by turbulent diffusion processes. These processes are highly complex in the combustion chamber and turbine, which is due to the boundary conditions in the combustor and the flow channels between the turbine blades. A simplified approach will be developed for estimating the turbulent mixing together with the standard averaged RANS-modeling. The mixing process of a manipulated partial flow will be investigated in turbulent combustors of different complexity in experimental (e.g. laser diagnostics) and numerical (CFD) ways. The experimental set-ups offer the possibility to manipulate the combustion process concerning flow velocity, temperature and exhaust gas concentration in a defined way.
Results
In the first funding period, it could be proved by numerical simulations that signatures of defects in combustor chambers are detectable in the exhaust jet. In the last period a simplified combustion chamber was developed to investigate defects and to determine the influence on the exhaust jet with different measurement techniques. In addition, CFD-models were tested and numerical calculations were conducted to simulate the flow and reaction processes. The simulated flow field was validated successfully by laser measurement techniques. These calculations allow both the investigation of further defects which cannot be implemented and experimentally evaluated and the intelligent associating of combustor errors and measured texture of the exhaust jet.

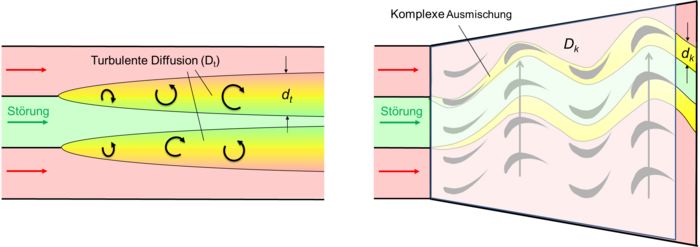
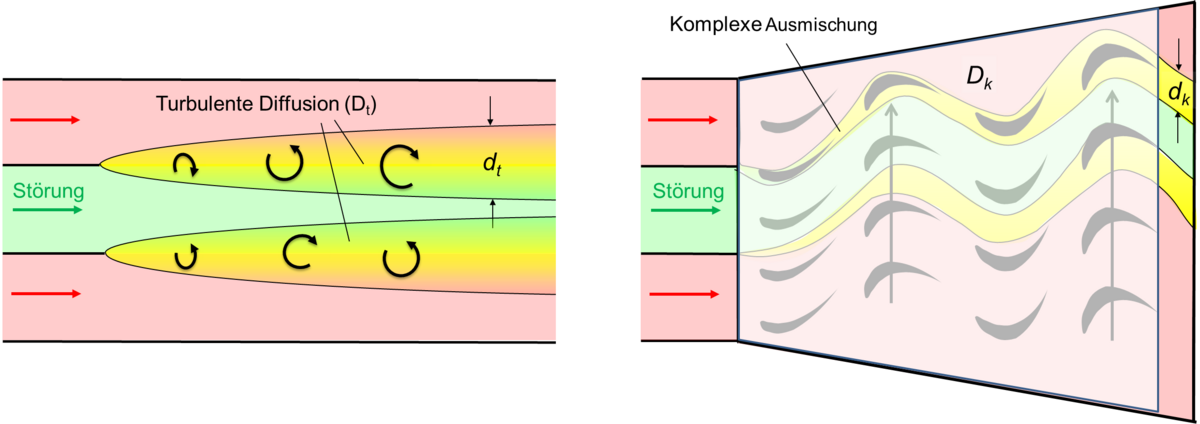
Current research and outlook
In the further course of the current funding period the validated model will be applied to a real combustor of an aircraft engine. The intention is to describe the impact of the mixing on the signature without increasing the required computing effort for the simulation. In order to apply the model to the processes in the turbine, it will also be tested with the RANS simulations of subproject A3. The improved modeling will be compared with the results of the BOS measurement technique behind the engine. The effect of the complex mixing on the signatures of combustor defects also influences the pattern recognition methodology, which is required for automatic associating of combustor defects and the damage library. With a realistic estimation of the mixing processes, the smallest detectable defects can be determined. The calculation of the reactive processes in combustion chambers is also of interest for other aircraft engines and stationary gas turbines and enables corresponding transfer projects. This also applies to the methodology to describe the mixing of signatures.

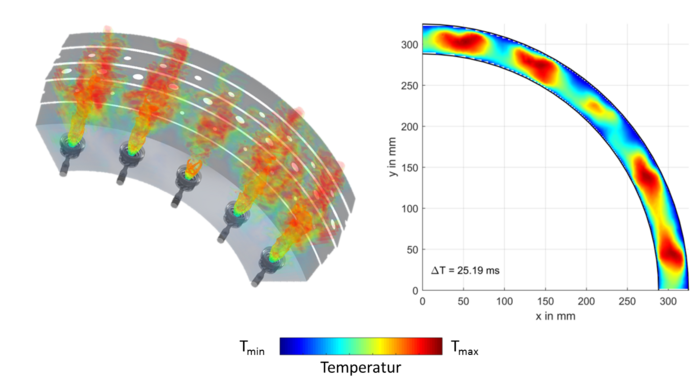
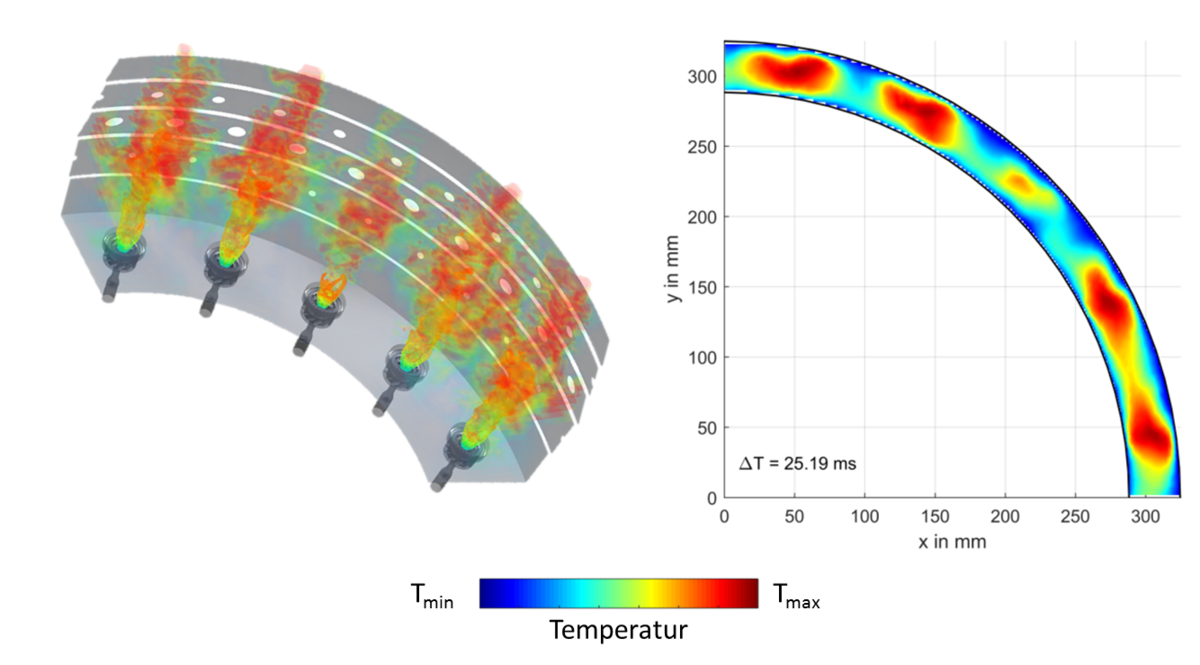
Subproject leader
30823 Garbsen
30823 Garbsen
Staff
Publications
International Conference Paper, peer-reviewed
-
(2019): Numerical Simulation of Gas Turbine Burning Chamber Combustion with Defined Burner Defects, Proceedings of the Global Power & Propulsion Forum (GPPF) 2019.
International Conference Paper, not peer-reviewed
-
(2019): Automatic Defect Detection in a Model Combustion Chamber Using Support Vector Machine., Portuguese Section of the Combustion Institute (Hg.): 9th European Combustion Meeting. Lisbon.
National Conference Paper, not peer-reviewed
-
(2021): Abschätzung der lokalen Schmidt-Zahl im turbulenten Mischungskanal mithilfe von neuronalen Netzen, 30. Deutscher Flammentag nachhaltige Verbrennung, Hannover, 28.-29.09.2021
-
(2019): Modellierung der turbulenten Diffusion anhand von Untersuchungen am Strömungskanal, 29. Deutscher Flammentag 2019
Books
-
(2018): Methodik einer Zustandsbeurteilung von Triebwerksbrennkammern, Garbsen: TEWISS (Berichte aus dem ITV)