Motivation and Objectives
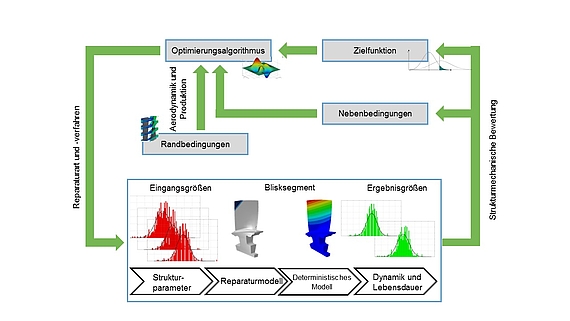


Decisions in the regeneration process are currently based mainly on subjective criteria. In most cases there are only generally stated repair limits. This engineering decision in the regeneration process will be supported by numerical optimization in the future. The decision about the geometry of the repair is achieved by a parameterized description. The basis for the optimization is a service life calculation, the parameterization of the repair and the use of efficient optimization algorithms.
Results
In the first funding periods it could be shown that geometric imperfections of jet engine blades significantly influence their structural behavior. From the statistical analysis of geometric data, changes in vibration amplitude and blade fatigue life could be identified. This allows the consideration of real geometrical tolerances in the calculating of the service life of the blade.
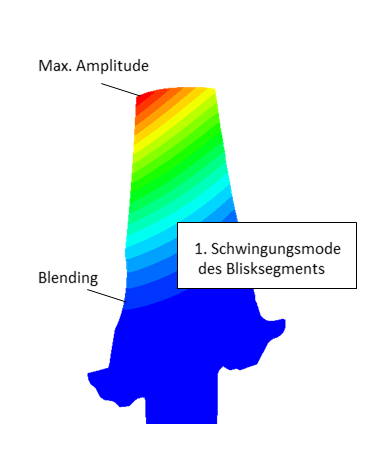
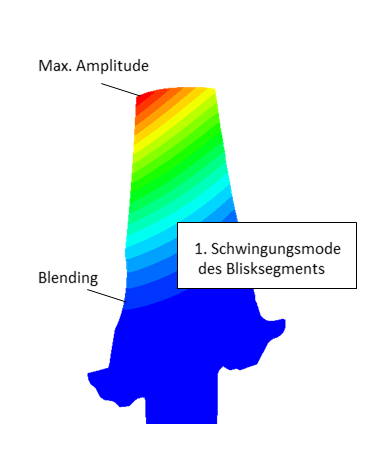
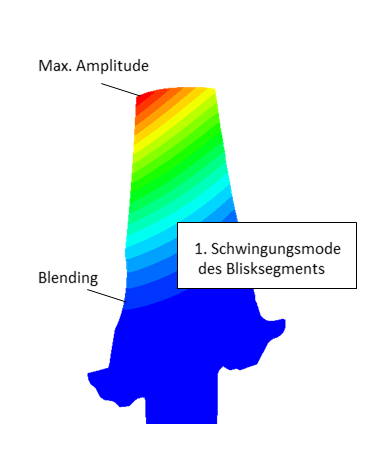
Current Research and Outlook
In the current research of the subproject the optimization potential of repair designs is analyzed. The optimization of blending and patch repairs of compressor blisks is based on parametric models and FE analyses. In addition to the ideal structure, the influence of scatter on the lifetime is considered. Competing repair targets are addressed by multi-objective optimization. The engineering decision about the repair design is supported by robust and reliability-based optimization. The repair designs optimized in the virtual path finally lead to an improved regeneration process in the real path.
Subproject leader
30167 Hannover
Staff
Publications
International Scientific Journal Paper, peer-reviewed
-
(2021): EngiO – Object-oriented framework for engineering optimization, Advances in Engineering Software 153 (1), S. 102959
DOI: 10.1016/j.advengsoft.2020.102959 -
(2021): Multiobjective Approach Toward Optimized Patch Repairs of Blisk Blades, AIAA Journal 22 (5), S. 1–12
DOI: 10.2514/1.J060723 -
(2020): A two-objective design optimisation approach for blending repairs of damaged compressor blisks, Aerospace Science and Technology 105, 106022
DOI: 10.1016/j.ast.2020.106022 -
(2018): Efficient structural analysis of gas turbine blades, Aircraft Eng & Aerospace Tech (Aircraft Engineering and Aerospace Technology) 90 (9), S. 1305–1316
DOI: 10.1108/AEAT-05-2016-0085 -
(2016): Probabilistic vibration and lifetime analysis of regenerated turbomachinery blades, Advances in Aircraft and Spacecraft Science 3 (4), S. 503–521
DOI: 10.12989/aas.2016.3.4.503 -
(2014): 3D multiscale crack propagation using the XFEM applied to a gas turbine blade, Comput Mech 53 (1), S. 173–188
DOI: 10.1007/s00466-013-0900-5
International Conference Paper, peer-reviewed
-
(2019): Parametric Design of Blisk Repairs by Patching Considering High Cycle Fatigue, In: ASME (Hg.): Proceedings of the ASME Turbo Expo 2019. Phoenix, USA: American Society of Mechanical Engineers, GT2019-90351
DOI: 10.1115/GT2019-90351 -
(2017): Influence of Blade Repairs on Compressor Blisk Vibration considering Aerodynamic Damping and Mistuning, GPPS (Hg.): Proceedings of Global Power and Propulsion Society Conference. Shanghai
-
(2011): The Influence of Blade Properties on the Forced Response of Mistuned Bladed Disks, ASME 2011 Turbo Expo: Turbine Technical Conference and Exposition, S. 1159–1170
DOI: 10.1115/GT2011-46826
National Conference Paper, not peer-reviewed
-
(2016): Fast Methods for Structural Analysis of Gas Turbine Blades with Manufacturing Imperfections, Deutscher Luft- und Raumfahrtkongress, Braunschweig 13. - 15. September 2016
-
(2012): Stochastische Untersuchungen regenerationsbedingter Imperfektionen einer Turbinenschaufel: Modellierung des deterministischen Modells zur effizienten Berechnung des Schwingungs- und Festigkeitsverhaltens, 5. Dresdner-Probabilistik-Workshop. Dresden, S. 1–11